Sustainable Aviation Fuel (SAF) is the umbrella term for all aviation fuels that, unlike conventional kerosene, are produced without the use of fossil feedstocks such as crude oil and also meet sustainability criteria. There are various processes for the production of SAF - both with biogenic and non-biogenic feedstocks.
SAF is a genuine alternative to fossil aviation fuel and is essential for the energy transition in aviation. SAF plays a central role in the Lufthansa Group's sustainability strategy.
SAF currently available and used by the Lufthansa Group is produced from biogenic residues such as used cooking oils using the HEFA process (Hydroprocessed Esters & Fatty Acids). CO2 is bound in the biogenic residues, which plants have previously removed from the atmosphere. When SAF is burned in the engine, only as much CO2 is emitted as was previously removed from the atmosphere by the source materials. The production and delivery process of SAF currently still generates CO2. Over its entire life cycle, SAF made from biogenic residues has a reduced CO2 footprint of around 80 percent compared to conventional kerosene made from fossil crude oil. The Lufthansa Group excludes palm oil-based raw materials for the production of SAF. The SAF used meets the requirements of the European Union's Renewable Energy Directive II (RED II), which sets strict sustainability criteria.
Production process of SAF from biogenic residues
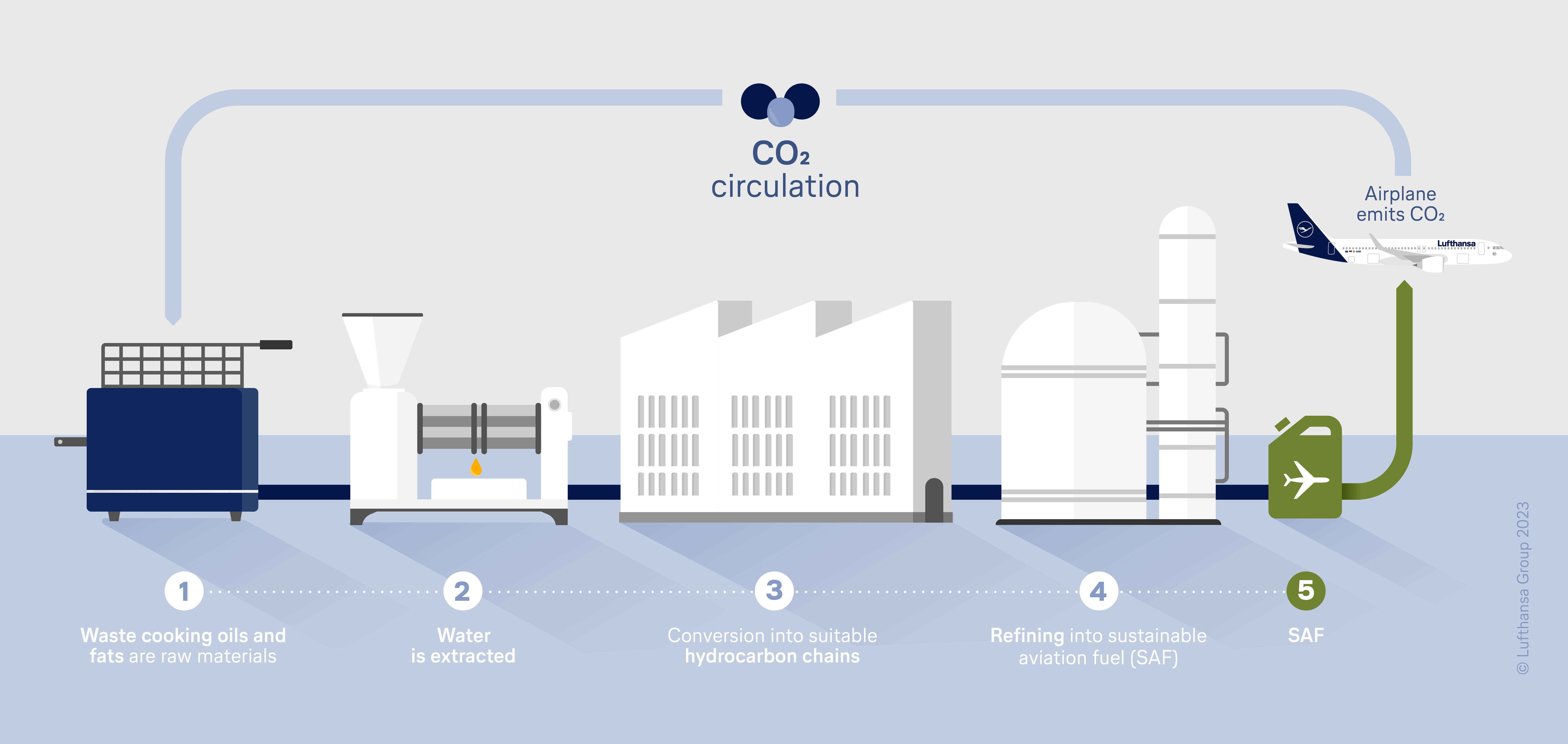
The Lufthansa Group is one of the largest SAF customers worldwide. However, the amount of SAF currently available on the global market is not yet sufficient to use large quantities in flight operations, and the price of SAF is significantly higher than that of fossil kerosene. According to the International Air Transport Association (IATA), only around 0.2 percent of the industry's global fuel requirements could be covered by SAF in 2023. SAF also accounted for around 0.2 percent of the Lufthansa Group's total fuel requirements in 2023. The Lufthansa Group wants to increase this share. The company is working on numerous projects worldwide to increase SAF availability, concluding MoUs with SAF manufacturers and examining options for long-term purchase agreements. At the same time, the Lufthansa Group is continuously expanding its offering for more sustainable travel for its customers. However, the aviation industry cannot initiate a self-sustaining market on its own. A targeted policy strategy is needed.
Next generation Sustainable Aviation Fuel
Due to the limited scalability of biogenic fuels, the Lufthansa Group is particularly committed to developing SAF technologies of the future. The focus here is on the forward-looking Power-to-Liquid (PtL) and Sun-to-Liquid (StL) technologies. These are currently still in the development phase towards large-scale industrial production. So far, PtL and StL aviation fuels are only available from test plants.
Power-to-Liquid
The Power-to-Liquid (PtL) technology uses renewably generated electricity, water and CO2 (for example from the atmosphere) to create a syngas from which SAF can be produced. PtL aviation fuels are currently still in the development stage towards industrial production.
This is how the Power-to-Liquid process works:
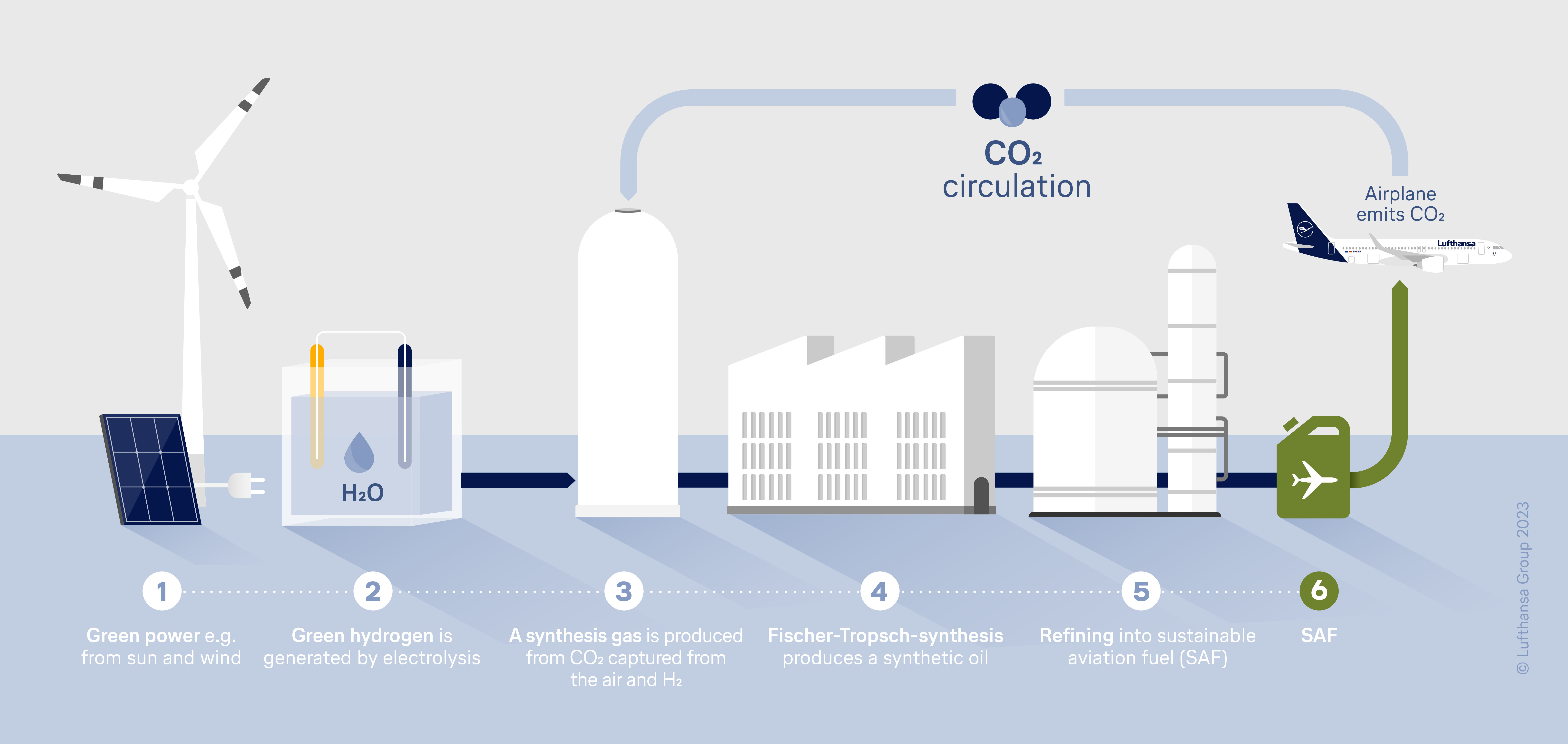
Sun-to-Liquid
The Sun-to-Liquid (StL) process is an innovative technology for producing SAF from high-temperature solar heat, water and CO2 (for example from the atmosphere). In 2022, the Lufthansa Group and the Group airline SWISS have agreed a strategic partnership with the Swiss-based company Synhelion for the market launch of Sun-to-liquid fuel. The aim of the partnership is to realize the first pilot projects in Europe and to scale up global production capacity. SWISS also plans to become the first customer of Synhelion's solar fuel.
This is how the Sun-to-Liquid process works:
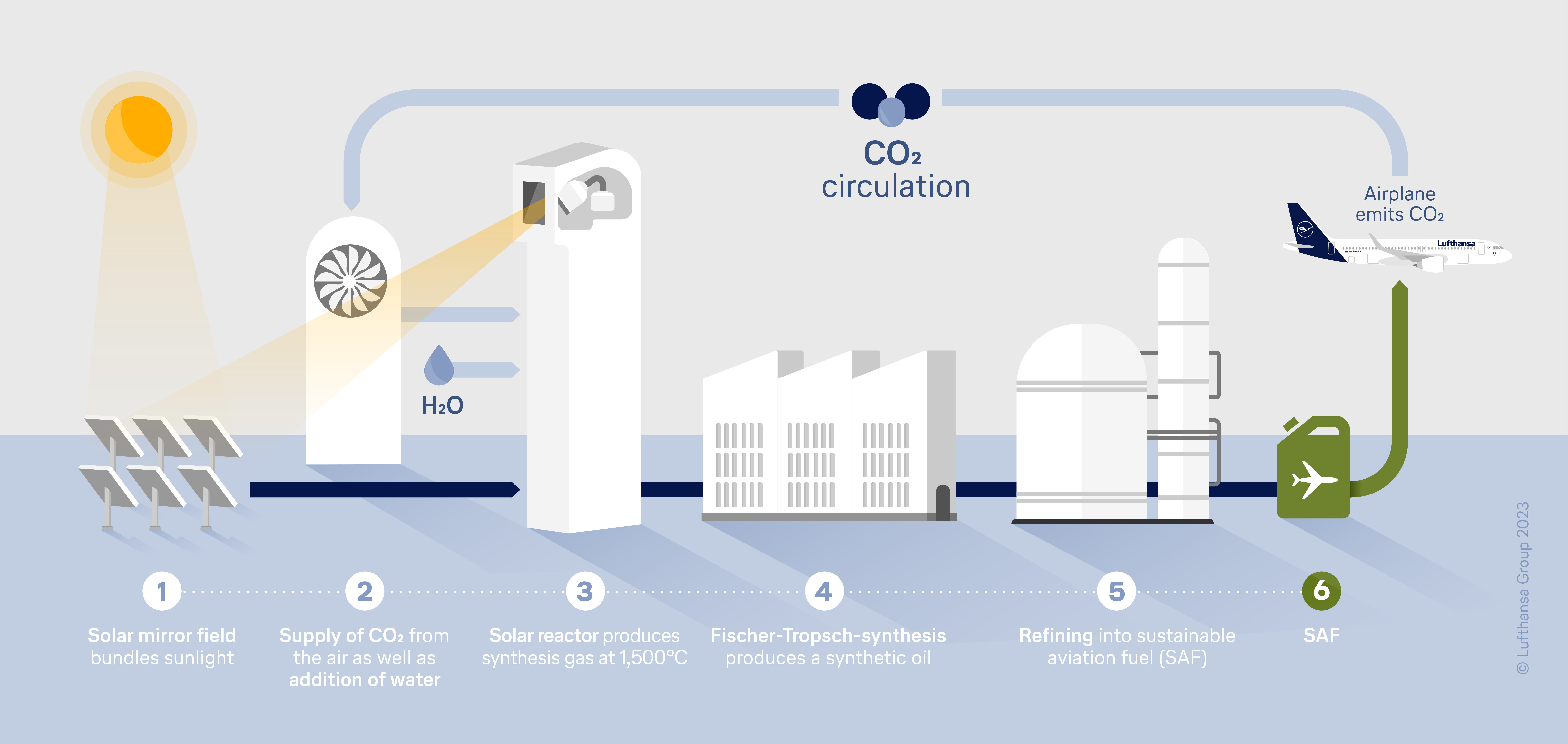
Pioneering achievement
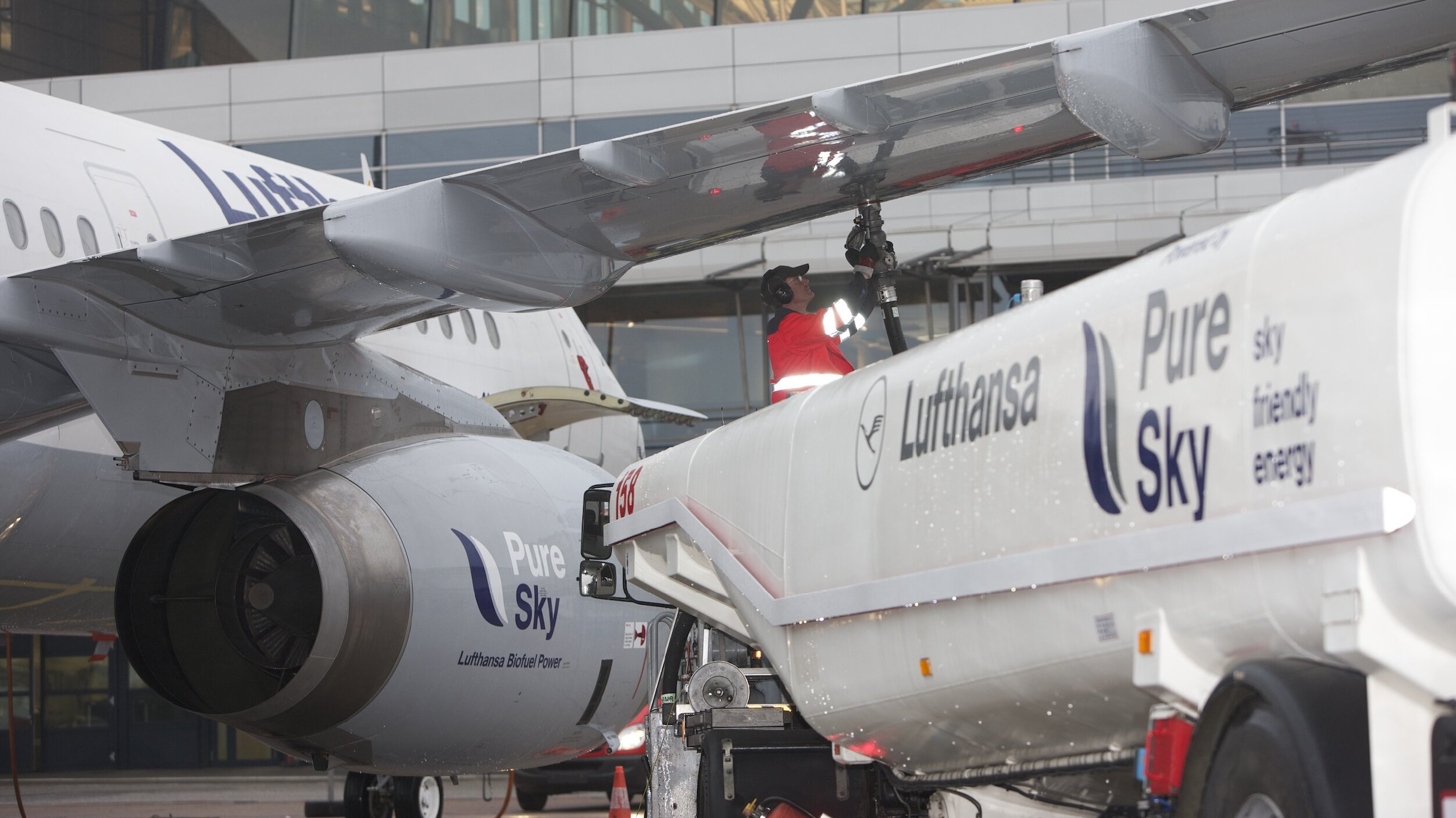
The Lufthansa Group has been committed to researching, testing, and deploying SAF for more than ten years and has built up an extensive network of partnerships. As early as 2011, Lufthansa tested SAF in regular flight operations for about six months. The result of the long-term testing was that it can be used without modification to the aircraft and without infrastructure adjustments. This is an enormous advantage of this technology.